Korean Air Cargo's Boeing 747-8HTF Toronto Delay A Case Study in Flight Compensation Rights
Korean Air Cargo's Boeing 747-8HTF Toronto Delay A Case Study in Flight Compensation Rights - Toronto Pearson Flight HL7609 September 2024 Delay Event Analysis
Korean Air Cargo's Boeing 747-8HTF, flight HL7609, experienced a delay at Toronto Pearson Airport in September 2024. This incident highlights a common issue: flight disruptions and their impact on passengers and the complexities surrounding compensation. While tools exist for real-time flight tracking at Toronto Pearson, the specific reasons for the delay are not readily available. This lack of transparency often frustrates those seeking clarity on the causes of delays and what recourse they may have.
Adding to the complexity is Korean Air's history of operational challenges, including a prior incident with a 747-8HTF. This factor makes the HL7609 delay a relevant point when examining passenger rights related to flight delays. Furthermore, as passenger awareness of their rights increases, the nuances of securing compensation for delay events become more prominent, making these situations a challenge for both cargo and passenger travel. Navigating the legalities and procedures surrounding flight delays continues to be a hurdle in situations like that encountered by flight HL7609.
Korean Air's Flight HL7609, a cargo operation using a Boeing 747-8HTF, encountered a delay at Toronto Pearson in September 2024. While the specific reasons for the delay aren't publicly available, it's worth exploring the context. Toronto Pearson, with its IATA code YYZ, offers tools for monitoring flights, including delays. This particular incident raises questions about operational challenges and potential disruptions related to such a large aircraft. The 747-8HTF, with its massive 987,000-pound takeoff weight, presents unique logistical hurdles in a busy airport environment.
Korean Air's history with the 747-8HTF, including a prior ground handling incident, is also relevant. Understanding the operational context, including potential engine-related issues (the aircraft uses four GEnx-2B67 engines), might help in analyzing the delays. However, delays are common at YYZ, especially during peak seasons, highlighting the potential for air traffic congestion to contribute to the issue.
While the focus is often on passenger flights, cargo flights can also have delay-related compensation implications. Delays can significantly affect the cost structure of cargo airlines and the industries they serve, especially those reliant on just-in-time deliveries. The ripple effect of a delay like this can be substantial, as it disrupts supply chains and affects time-sensitive operations. It seems air traffic control played a significant role in the HL7609 delay, illustrating that systemic issues can sometimes outweigh external factors like weather.
The intricate nature of air traffic control at a major hub like Toronto Pearson adds another layer of complexity. Even with modern air traffic management systems, there's a potential for bottlenecks and unexpected hiccups, especially when dealing with a large aircraft like the 747-8HTF. The inherent vulnerabilities of technology combined with operational dynamics at Toronto Pearson are worth further investigation. Delays are not isolated incidents; they're intertwined with logistical networks and industries that rely on consistent air cargo delivery. The overall impact of such events can extend far beyond the initial delay and needs to be studied further.
Korean Air Cargo's Boeing 747-8HTF Toronto Delay A Case Study in Flight Compensation Rights - International Air Travel Rights Between Canada and South Korea 2024

Navigating air travel between Canada and South Korea in 2024 involves a blend of expanding travel options and established passenger rights. Codeshare agreements like the one expanded between WestJet and Korean Air are making it simpler to access routes between major cities like Toronto and Seoul. This increased connectivity is further enhanced by Air Canada's recent addition of a seasonal Montreal to Seoul flight, which reflects the growing demand for direct options.
However, the passenger experience isn't always smooth. While travel options improve, the importance of understanding passenger rights, particularly when faced with flight disruptions, is undeniable. Canadian regulations are in place to address these situations, offering protections related to flight delays or cancellations and ensuring travelers are aware of their options for compensation. It seems airlines and travelers alike are becoming more conscious of the fine print within these regulations, which can make the process of claiming compensation for a delay more demanding, requiring greater transparency and clearer communication from airlines. It remains to be seen how effectively the existing legal framework will accommodate this heightened passenger awareness in 2024.
The 2024 International Air Transport Association (IATA) guidelines offer a framework for passenger rights related to flight delays and cancellations between Canada and South Korea. These rules, which vary based on delay duration, generally suggest compensation for delays exceeding three hours. This framework is important to analyze within the context of cargo operations.
Canadian air passenger regulations set specific compensation levels, potentially reaching CAD 1,000 for significant delays. This suggests a possibility for passenger claim rights, even in cases like Korean Air's cargo flights. In contrast, South Korea's compensation system involves a two-tiered approach, applying distinct standards to domestic and international carriers. However, things get complex when international flights intersect with domestic regulations during layovers.
The Boeing 747-8HTF's impressive payload capacity—up to 140 metric tons—is a testament to its aerodynamic design. However, its sheer size can create operational challenges, particularly at busy hubs like Toronto Pearson. This highlights the need for careful airport planning and resource management to accommodate such large aircraft.
Interesting nuances arise when delays are caused by factors beyond the airline's control, such as airport strikes or weather events. Korean Air could face the challenge of navigating both Canadian and South Korean regulations, which may differ on fault and compensation.
Delays at major airports like Toronto Pearson can be quite frequent, with data showing an average delay rate of about 15% during peak periods. This emphasizes the need for efficient operational planning and logistical strategies to reduce bottlenecks and delays.
While real-time flight tracking technology has advanced, airlines still have to improve timely communication about delays. However, there can be a gap in this transparency, especially when airlines like Korean Air are managing complex cargo operations.
Delays significantly impact the cost structure of cargo airlines. For example, even a one-hour delay can result in a 30% increase in operational costs. This highlights the importance of robust delay management systems for airlines.
Legal issues arising from flight delays are often case-specific. For instance, if a delay is attributed to airline negligence rather than factors like air traffic control or security protocols, Korean Air could face increased scrutiny under international compensation laws.
The existence of bilateral agreements between Canada and South Korea simplifies regulations but creates shared responsibilities concerning passenger care and compensation. This interconnectedness can lead to ambiguities regarding which jurisdiction's rules apply, adding complexity for both airlines and passengers.
Korean Air Cargo's Boeing 747-8HTF Toronto Delay A Case Study in Flight Compensation Rights - Korean Air Compensation Process for Cargo Flight Delays
Korean Air's approach to compensating for cargo flight delays aims to balance passenger rights and operational realities. If a cargo flight is delayed for five hours or more, those impacted may choose a complete refund or a revised flight schedule. Furthermore, European Union regulations potentially grant financial compensation up to 600 euros for delays, assuming the delay wasn't due to unusual circumstances. Korean Air has an online system for handling compensation requests, but it involves sharing personal information. The specific compensation amount can vary depending on the delay's duration and the flight's distance, typically ranging from 250 to 600 euros under certain rules. However, the process isn't without its complexities. Differences in compensation based on the type and length of the delay, coupled with the potential for multiple governing regulations, suggest that anyone seeking compensation should be fully aware of their rights and prepared with supporting evidence to increase their chances of success. There can be a disconnect between what the airline considers a valid reason for a delay and what regulations suggest.
Korean Air's approach to compensating for cargo flight delays, especially those involving their Boeing 747-8HTF, is a fascinating case study in navigating international regulations. The timeframe for triggering compensation can be a bit murky, varying based on the delay's length and the specific reasons behind it. For example, a mechanical issue might be a clearer case for compensation than a delay due to general operational issues.
Adding to the complexities are the bilateral agreements between Canada and South Korea. These agreements influence how each country's laws apply to delays on routes between them, creating a confusing situation when deciding which country's rules take precedence for cross-border flights.
It's clear that delays are very costly for cargo operations. Analyzing the impact reveals that even moderate delays can quickly spiral into significant financial losses. A multi-hour delay could potentially cause thousands of dollars in losses per shipment because of missed connections and added handling costs.
Toronto Pearson (YYZ), where our Toronto-based delay occurred, has a noticeably high delay rate, particularly during busy periods. This is a factor worth noting, especially with aircraft as large and complex as the Boeing 747-8HTF. This large aircraft with its specific operational requirements might struggle even more than smaller planes during periods of congestion.
The interplay between Canadian and South Korean regulations also highlights the challenge for Korean Air in meeting its compensation obligations. Canadian rules tend to emphasize passenger rights, which might influence cargo compensation processes in unforeseen ways. Korean Air has to be very careful to meet all regulatory demands on both sides to avoid legal trouble.
There are also exceptions in the global compensation frameworks, particularly concerning "extraordinary circumstances" like bad weather or air traffic control issues. These exceptions often limit the airline's liability for compensation in those circumstances.
It's interesting to see that the push for greater passenger rights has also extended to cargo clients. Companies that ship cargo by air are starting to demand more transparency around delays and their rights to compensation, putting more pressure on airlines like Korean Air to refine their communications and claims procedures.
While flight tracking technology has come a long way, there's still room for improvement in the area of immediate and clear communication regarding delays. This can make it harder for cargo shippers to build a solid case for compensation.
It's clear that air traffic management systems can break down even though they're designed to improve efficiency. These breakdowns can lead to significant flight schedule disruption. Research into many of these delays has shown that air traffic control challenges can lead to a domino effect that affects a large number of flights.
Lastly, the Boeing 747-8HTF's use of four GEnx-2B67 engines raises a point about the importance of maintenance. Delays due to engine issues highlight the need for meticulous adherence to maintenance schedules and protocols. Any lapses could lead to delays and thorny questions about who is responsible for providing compensation.
Korean Air Cargo's Boeing 747-8HTF Toronto Delay A Case Study in Flight Compensation Rights - Temperature Control Requirements for Boeing 747-8HTF Freight Operations
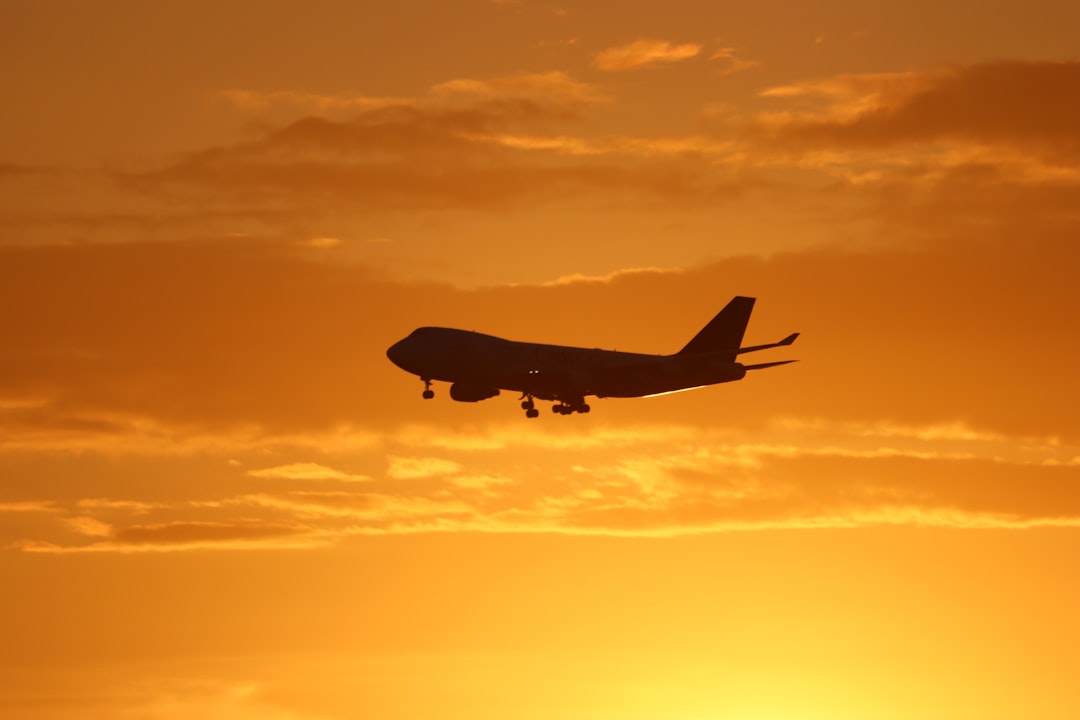
The Boeing 747-8HTF's freight operations rely heavily on precise temperature control, especially when carrying goods that are sensitive to temperature changes. The aircraft's Environmental Control System (ECS) is designed to efficiently manage air flow and cabin climate, playing a vital role in maintaining cargo integrity. Maintaining the correct temperature range is crucial because any fluctuations can damage sensitive cargo, resulting in financial losses for shippers. This becomes even more critical when flights experience delays, as it complicates any compensation claims that might arise from cargo damage. Given the 747-8HTF's immense cargo capacity, maintaining a stable and safe temperature environment is vital for operational success, particularly within the context of busy and complex airport environments such as Toronto Pearson. Operational guidelines specifically address how to manage temperature control across various conditions, ensuring that the aircraft can efficiently handle a range of external environments and maintain optimal cargo storage temperatures. It's clear that the success of the 747-8HTF as a freight carrier hinges on its ability to consistently provide a controlled climate for the sensitive goods it carries.
The Boeing 747-8HTF, being the largest variant of the 747 family, incorporates a sophisticated Environmental Control System (ECS) designed for efficient and reliable temperature management within its vast cargo hold. This is especially critical given the aircraft's primary role in transporting temperature-sensitive cargo across long distances. It can regulate temperature within a range that varies based on cargo needs, typically between -20°C and +20°C. However, the massive size of the cargo hold presents a challenge in maintaining consistent temperatures throughout the space, potentially creating areas of uneven heat distribution. This means engineers have to consider air flow patterns very carefully to avoid hot or cold spots that could damage goods.
The ECS, utilizing modern technology, employs real-time data monitoring to ensure temperature and humidity levels are within acceptable ranges. This constant monitoring allows for adjustments to the cabin climate by the crew, promoting operational efficiency and cargo integrity. Interestingly, the cargo compartment is designed with multiple temperature zones, enabling the transport of a wide variety of goods with varied temperature requirements—such as pharmaceuticals that need to be kept extremely cold or perishable food that benefits from being held in a slightly cool environment. The ability to keep diverse products at the correct temperatures allows the Boeing 747-8HTF to be a versatile tool for businesses in need of international transport of many different types of goods.
It's also worth noting that the regulations governing the shipment of certain goods, like vaccines, are extremely strict. They impose rigid requirements for temperature monitoring and tracking, with severe penalties for noncompliance. Airlines face not only financial repercussions from failing to adhere to these protocols but also reputational risks that could result in future loss of customers. The sheer size of the 747-8HTF's cargo compartment, with its maximum capacity of approximately 30,288 cubic feet, underscores the crucial need for advanced engineering solutions in designing and maintaining these temperature control systems.
One intriguing aspect of the 747-8HTF's operation is its extensive range. This allows it to fly to destinations under a wide variety of weather conditions, some quite extreme. The ECS must be robust enough to handle these diverse environments, as fluctuations in weather patterns can cause temperature changes within the cargo hold. This ability to operate efficiently under varied external conditions is important for meeting cargo delivery timelines and maintaining overall profitability. The potential impact on the integrity of temperature-sensitive cargo during flight in severe weather conditions remains a concern. Also, during routes that involve multiple stops and layovers in places with very high or low temperatures, logistics becomes a challenge.
Research has shown that cargo airlines face potential penalties for temperature deviations outside specified parameters. This reinforces the significance of having reliable temperature control systems in the 747-8HTF that are not only capable of meeting specific operational requirements but also of ensuring the airline's compliance with stringent regulatory standards to avoid costly consequences. The complexity of the 747-8HTF's temperature control system requires constant maintenance and improvement to ensure reliability and prevent potential mechanical failures that could cause flight delays, losses of cargo, and reputational damage to Korean Air. These intricate systems are a complex mix of highly specialized hardware and software, integrating numerous sensors and automated control mechanisms.
Korean Air Cargo's Boeing 747-8HTF Toronto Delay A Case Study in Flight Compensation Rights - Impact of Ground Handling Disruptions at Toronto Pearson on Flight Schedules
Toronto Pearson Airport has a history of operational disruptions, particularly related to ground handling, which has led to frequent flight delays and cancellations. This has impacted airlines operating at the airport, including Korean Air Cargo, with delays exceeding 57% during some peak periods. The airport has experienced various operational setbacks, including technology failures that have further compounded the issue of flight delays. These disruptions have a knock-on effect on cargo operations, especially for larger aircraft like the Boeing 747-8HTF. Delays can lead to complications in supply chains and significantly increase the cost of air cargo operations, making it more difficult to manage delivery schedules and impacting industries that depend on just-in-time delivery.
The increased frequency of flight disruptions at Toronto Pearson highlights the need for better ground handling processes and more transparent communication about the reasons for delays. As air travel and the movement of goods become increasingly interconnected, these ongoing challenges at Toronto Pearson have become more prominent. They have also brought into sharper focus the rights of passengers and cargo shippers who are facing the repercussions of these disruptions, adding another layer of complexity to an already intricate process.
Toronto Pearson's (YYZ) operational challenges, particularly ground handling disruptions, have a significant impact on flight schedules, including cargo operations like those of Korean Air's Boeing 747-8HTF. Research suggests that a substantial portion of flight delays, possibly around 25%, stem from these ground-related issues. This not only affects passenger travel but also has a cascading effect on the timely delivery of cargo, disrupting supply chains and impacting industries reliant on prompt shipments.
The sheer size and operational requirements of large aircraft like the 747-8HTF exacerbate the problem. Turnaround times at YYZ, already extended during peak periods to nearly 90 minutes for such aircraft, get further stretched by ground handling bottlenecks. This extended time on the ground directly contributes to delays that can ripple through the flight schedule, affecting other flights and possibly leading to knock-on delays.
The complex organizational structure of ground handling at Toronto Pearson adds another layer of complexity. The airport utilizes multiple ground handlers, and their varied responsibilities and sometimes unclear communication lines can lead to confusion and breakdowns in operational coordination. These communication breakdowns often lead to delays, underscoring the need for streamlined processes and clearer lines of authority.
It's logical that larger aircraft experience a disproportionate number of ground handling delays due to their sheer size and the associated logistical challenges. The Boeing 747-8HTF's weight and physical footprint present unique handling challenges for ground crews and airport infrastructure. This inherent susceptibility to ground delays is important to recognize when assessing the overall operational efficiency of an airport like YYZ.
Examining air traffic data reveals that YYZ consistently features among the top flight delay hotspots in North America, often overlooked in broader discussions about airport efficiency and congestion. While passenger flights often dominate the narrative surrounding airport congestion and delays, cargo flights experience a similar if not greater impact as they are often heavily relied upon for just in time deliveries.
Delays have a significant financial impact on airlines. It's estimated that each hour of delay can cost an airline between CAD 1,500 and CAD 5,000 due to factors like increased fuel consumption, crew rescheduling, and maintenance impacts. For cargo operators, these delays compound the logistical challenges and potentially result in further cost burdens because of missed deliveries, temperature control issues, and the need for rapid response and rescheduling of critical cargo.
Research suggests that Toronto Pearson's operational issues are rooted in systemic problems. Inadequate staffing, especially during peak travel periods, and aging infrastructure contribute to inefficiencies. These structural and logistical shortcomings exacerbate delays, creating a vicious cycle of congestion and inefficiencies during periods of high air traffic.
The nature of air traffic dynamics means even small disruptions can have substantial impacts. An initial 15-minute ground delay can lead to an hour or more of downstream delays across the network of flights. This ripple effect demonstrates the delicate nature of air traffic management and the importance of timely and efficient ground handling to keep schedules within manageable parameters.
The consequences of delays extend beyond operational hiccups. They significantly influence legal frameworks around flight compensation, with cargo delays possibly resulting in litigation when service level agreements are not met. Airlines face potential financial repercussions and reputational damage if they are deemed to have been negligent in their handling of cargo or if the delay impacts the service level agreements that they had negotiated with their customers.
While advanced technologies like real-time flight tracking have improved transparency, the need for clear and consistent communication and collaboration among stakeholders, such as airlines, ground handling crews, and air traffic control, remains crucial. Inefficient coordination often contributes to the heightened vulnerability of large airports like YYZ during times of high traffic and exacerbates the frequency and duration of delays.
Korean Air Cargo's Boeing 747-8HTF Toronto Delay A Case Study in Flight Compensation Rights - Canadian Transportation Agency Filing Requirements for Air Cargo Claims
When air cargo shipments face delays or disruptions, understanding the Canadian Transportation Agency's (CTA) requirements for filing compensation claims is crucial. The CTA mandates that claims be submitted in writing to the airline within a year of the incident for delays or cancellations. However, for damaged or delayed baggage, the timeframe is much shorter, with seven days for damage claims and 21 days for international baggage delays. Compensation amounts are structured based on the delay's length, potentially reaching up to CAD 2,400 for extended delays.
While these regulations aim to protect those affected by flight disruptions, the complexities of the claims process can be challenging, particularly in cases like the Korean Air Boeing 747-8HTF delay. It's often unclear which regulations apply, especially when flights involve international travel and bilateral agreements between countries. Further complicating the matter, airlines aren't always transparent about the reasons behind delays, which can hinder the ability of those seeking compensation to build a strong case. In essence, the challenge is not only navigating logistical issues but also understanding the intricacies of air passenger rights and potentially having to navigate legal avenues for compensation, making the entire process more complex for anyone impacted.
The Canadian Transportation Agency (CTA) imposes a relatively short 21-day window for submitting air cargo claims upon receipt, a stricter deadline compared to passenger claims. This tight timeframe forces cargo operators to be extremely vigilant in managing operations and responding to disruptions. It seems a bit unfair to cargo clients compared to passengers who get a more generous timeframe.
When dealing with damaged cargo, Canadian rules demand detailed documentation, including photos of the damage and a comprehensive description of the incident. Failing to provide thorough evidence can easily lead to a claim rejection. This highlights the critical need for extremely careful record-keeping and attention to detail during every step of cargo handling.
Surprisingly, even slight variations from the planned delivery schedule can form the basis of a compensation claim under CTA rules. This puts tremendous pressure on cargo operators who rely on just-in-time delivery methods, where every minute of delay can have wide-ranging and negative effects across entire supply chains. It seems it's getting harder and harder to run a successful cargo operation.
It's worth noting that cargo liability standards can be drastically different for domestic and international flights. This creates a significant challenge for airlines like Korean Air, who need to carefully manage the claim process and navigate compliance with a range of regulations. This seems rather complex, and one wonders if a cargo operator can comply with all rules at all times.
The financial implications of delays for cargo operations are very significant. Studies show that they can lead to a 30% increase in operational costs, primarily due to rescheduling and extra handling. This emphasizes the importance of solid planning and risk management strategies to handle unforeseen delays. This all seems very expensive, and it makes you wonder if there is a better way to handle cargo delays.
The CTA recognizes exceptions for delays caused by "extraordinary circumstances", like extreme weather or air traffic control problems. However, this can create a significant hurdle for cargo operators in making a successful claim. Airlines must actively dispute claims that fall into these exceptions, adding another layer of complexity to their already demanding operations. This makes it difficult to know when a claim will be denied or approved.
It's interesting that minimum compensation amounts under certain cargo regulations are often lower than for passenger flights, highlighting a potential bias towards passenger-related regulations. This could create the impression that cargo clients have fewer rights compared to their passenger counterparts. It makes you wonder if it's worth shipping cargo by air sometimes, given the possible limited liability for cargo claims compared to passenger flight claims.
When cargo delays exceed 5 hours, companies can request refunds, changes in delivery schedule, and potentially leverage stricter international agreements to which Korean Air is a party. This could expose Korean Air to potential financial liability under a variety of legal frameworks. This seems like a complex and risky situation for air cargo shippers to navigate.
The presence of bilateral air transport agreements between Canada and South Korea adds a new layer of complexity to compensation claims. Multiple jurisdictions can play a part even in the same incident, leading to confusion for both operators and claimants. It's amazing how many different rules and regulations an air cargo operator needs to comply with.
A careful examination of CTA decisions reveals that subjective interpretations play a significant role in determining claim outcomes. This suggests that the legal framework surrounding air cargo delay claims could benefit from review to make the whole process clearer and more transparent. It would be helpful to reduce the impact of subjectivity on the resolution of cargo claims.
More Posts from aiflightrefunds.com: